R&D Tax Credits For The Manufacturing Sector
Get the sector experience you need to make a successful R&D tax relief claim
QLC helps manufacturing companies accelerate their R&D claims with our streamlined portal and expert team.
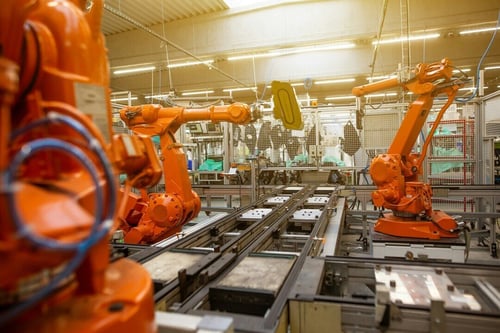
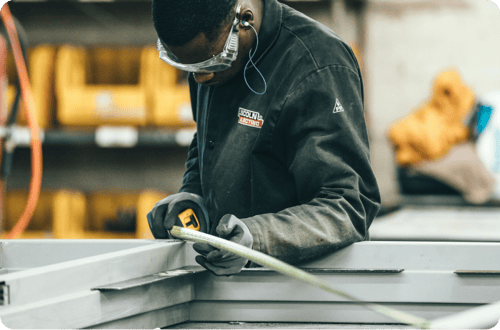
Our manufacturing experience
With many years of experience helping manufacturing companies take advantage of R&D tax incentives, QLC understands the unique challenges and opportunities in your industry. We've helped many manufacturing businesses claim millions in R&D tax credits. Let QLC help you.
Find out more in our manufacturing sector success stories below:
Manufacturing R&D Tax Relief success stories
See how we help manufacturing companies leverage R&D tax relief to innovate, improve machinery performance and reduce costs.
CASE study 1
Maximising machinery efficiency
R&D innovations in plastic injection, paper rolling and printing equipment
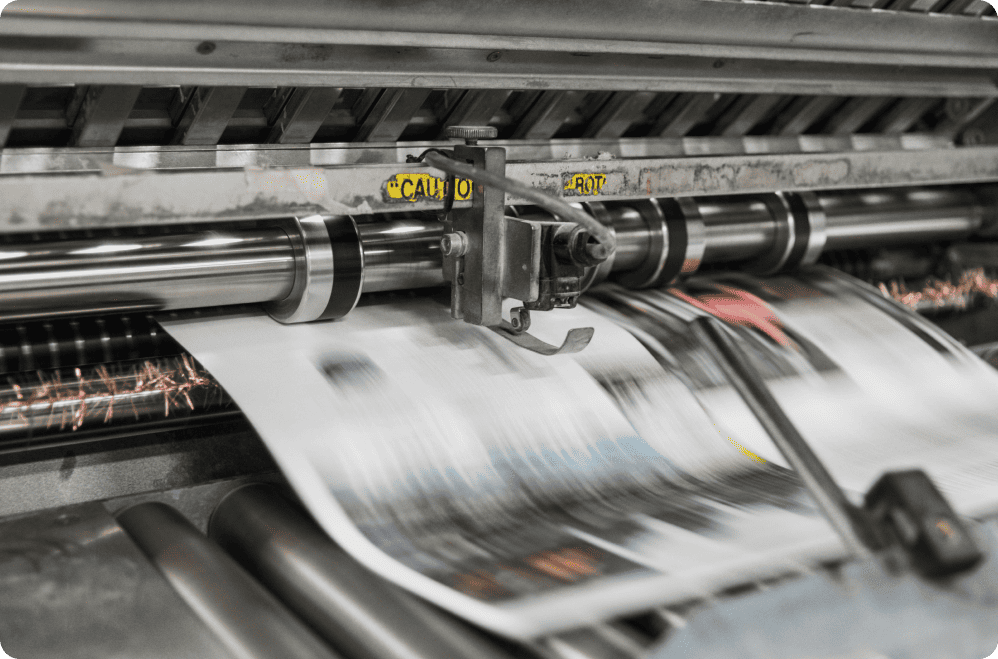
Our client, like many in the manufacturing industry, faced the challenge of boosting machinery performance without the significant expense of new equipment. To overcome this, they embarked on a series of R&D projects aimed at enhancing their existing machinery's capabilities. We collaborated closely, taking a comprehensive approach that tackled each problem in stages. These sub-projects not only delivered targeted improvements but also laid the foundation for future innovations.
Improving plastic injection moulding machines
A key focus was enhancing the efficiency of their plastic injection moulding machines. The goal was simple: increase the flow of pellets through the system to streamline production. The client designed and prototyped a 'collar follower' to integrate into the existing machinery, but the initial versions caused pellet contamination. This setback led to further iterations and material testing. After several adjustments, the final solution significantly improved performance, demonstrating the value of persistence in the R&D process.
Reducing manual intervention in paper rolling machines
Another critical project aimed to reduce the frequent manual intervention required for their paper rolling machines. Paper frequently stuck to the rollers, causing disruptions. To solve this, the client tested different materials and roller designs, refining prototypes until they found a solution that not only reduced maintenance but also increased the machine's overall efficiency. The result? Smoother production, less downtime and fewer manual fixes.
Lowering costs for paper printing machinery
Finally, the client sought to reduce the manufacturing costs of their paper printing machines without sacrificing performance. By exploring the existing structure, they developed a lighter, more efficient design. Rigorous testing ensured that safety and functionality were maintained, while production costs were significantly lowered—proving that innovation doesn’t have to come at a financial premium.
The results: success
Each sub-project yielded measurable improvements to the client’s machinery, establishing new benchmarks for the industry. Because such advancements were not readily available in the public domain, the work qualified as R&D, allowing the client to claim valuable tax credits. With these funds, they are now reinvesting in future innovation—proof that optimising existing equipment can be both cost-effective and growth-driven.
With QLC's help, they successfully claimed R&D tax credits for these projects, securing vital funds to reinvest in further innovation. This case exemplifies how investing in R&D for machinery improvements can be a cost-effective alternative to purchasing new equipment, all while enhancing efficiency and driving growth.
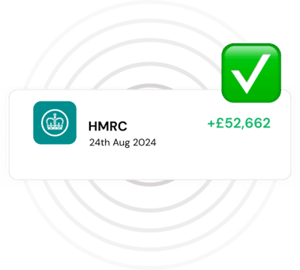
CASE study 2
Innovating large-scale milling
Portable machine development for oversized workpieces
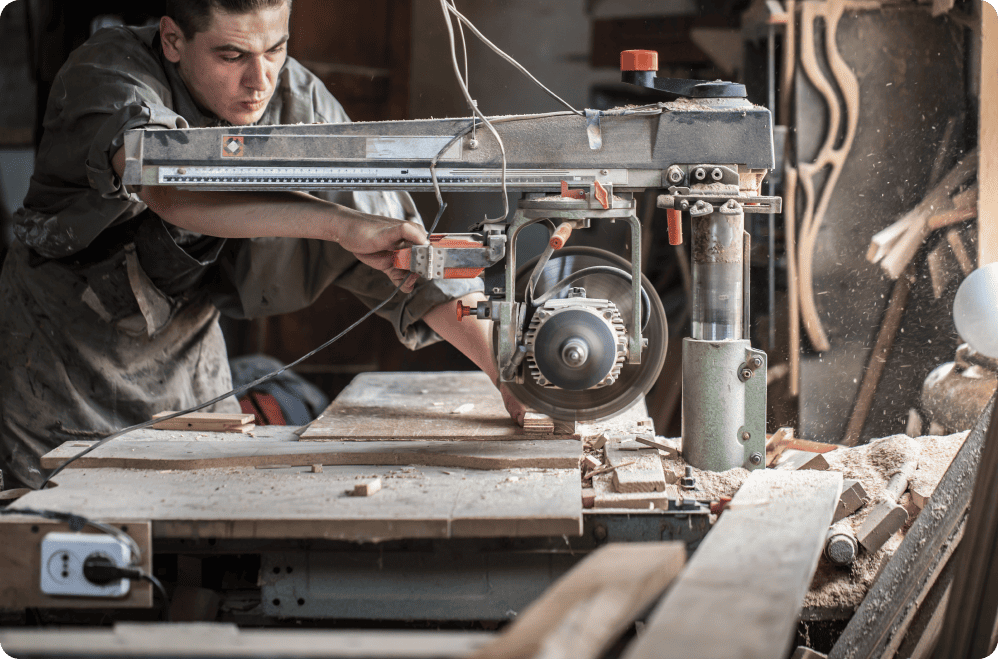
Our client embarked on an ambitious project to develop a milling machine with enhanced capabilities, specifically designed to manufacture supporting beams used atop large doors, like those found in airports. These beams, measuring 13 metres long with custom-drilled slots, posed a significant challenge for existing milling machines, which lacked the capacity to handle such large workpieces. The engineers sought to create a machine that could overcome this limitation, making the project a perfect candidate for R&D.
Designing a machine for oversized workpieces
A conventional solution would have been to design a machine with an oversized bed and spindle to accommodate the larger beams. However, this approach would have resulted in an excessively large and impractical machine. Since portability was also a key requirement for the client, this solution was ruled out early on. Instead, the engineers focused on an innovative alternative—adjusting the workpiece itself to allow the machine to handle the larger beams while keeping the machine compact.
Innovating to reduce machine size without compromising functionality
Through extensive trials and experimentation, the engineers developed a unique method of holding the workpiece that allowed it to be processed in smaller sections. Alongside this, they engineered a new cutting technique to improve the efficiency of machining the slots. However, the initial trials affected the tolerances, prompting further design iterations to develop a holder that could support the machine and maintain the required precision.
The results: a portable, high-capacity milling machine
Ultimately, the project resulted in a breakthrough—a milling machine that could work on large workpieces, remained portable and maintained the precision of traditional, larger machines. This innovation not only solved the client’s manufacturing challenge but also represented a clear advancement over the existing machines available at the time.
By partnering with QLC, our client was able to claim R&D tax credits for their innovative work on developing a portable milling machine capable of handling oversized workpieces. This funding allowed them to reinvest in further advancements, ensuring they continue to lead in machinery innovation without the financial burden of such ambitious projects.
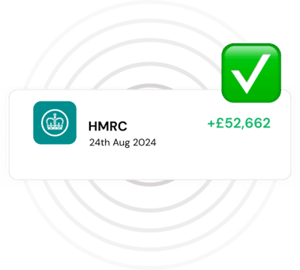
CASE study 3
Enhancing Tooling Efficiency
Redesigning a press mould machine for improved longevity and performance
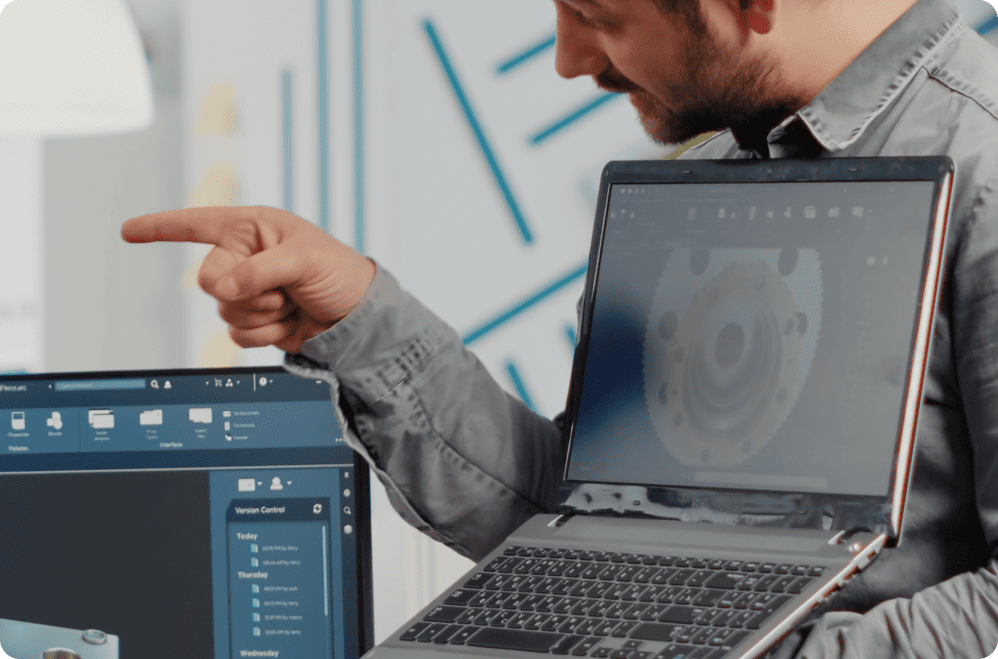
Our client set out to significantly enhance the lifespan and functionality of a tooling component used in producing angled coupling parts for underground sewer pipes. The existing component had design flaws that limited its efficiency and durability. The company identified the replacement of the existing inclined pin actuators within the mould tool as a key step toward improving both the pressing process cycle speed and the overall lifespan of the tool.
Redesigning mechanical elements for improved performance
The goal was ambitious: to fundamentally alter the mechanical elements of the press mould machine while simultaneously extending its lifespan and increasing its cycle rate. By replacing the inclined pin actuators with a hydraulic cylinder, the engineers aimed to create a more robust, efficient system. This transformation required more than just swapping components; it involved reconfiguring the tooling entirely to integrate the new, bulkier hydraulic system.
Overcoming challenges in system integration
The introduction of the hydraulic cylinder presented significant design challenges. Ensuring the machine maintained its functionality while incorporating this new component required a complete reorientation of the machine. The team developed several models, calculating and adjusting the machine’s clearances and adding ancillary parts to support the new system. The reconfiguration also included adapting the press core to the hydraulic cylinder and avoiding component extrusion, ensuring the machine operated smoothly despite the substantial changes.
The results: enhanced tooling and increased efficiency
By the end of the project, the client had achieved their goal—a vastly improved version of the original press mould machine. The new design not only extended the tool’s lifespan but also allowed for increased cycle speeds, making the process more efficient and reliable.
With QLC’s help, our client successfully claimed R&D tax credits for their pioneering redesign of a press mould machine. This not only rewarded their efforts to improve tooling efficiency and longevity but also freed up vital funds to reinvest in future mechanical enhancements, driving continued innovation in their field.
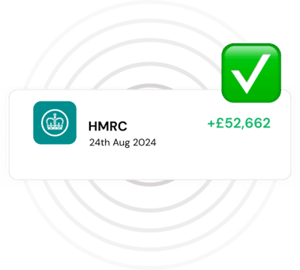
CASE study 4
Innovating machinery efficiency
R&D Success in plastic moulding, paper rolling and printing
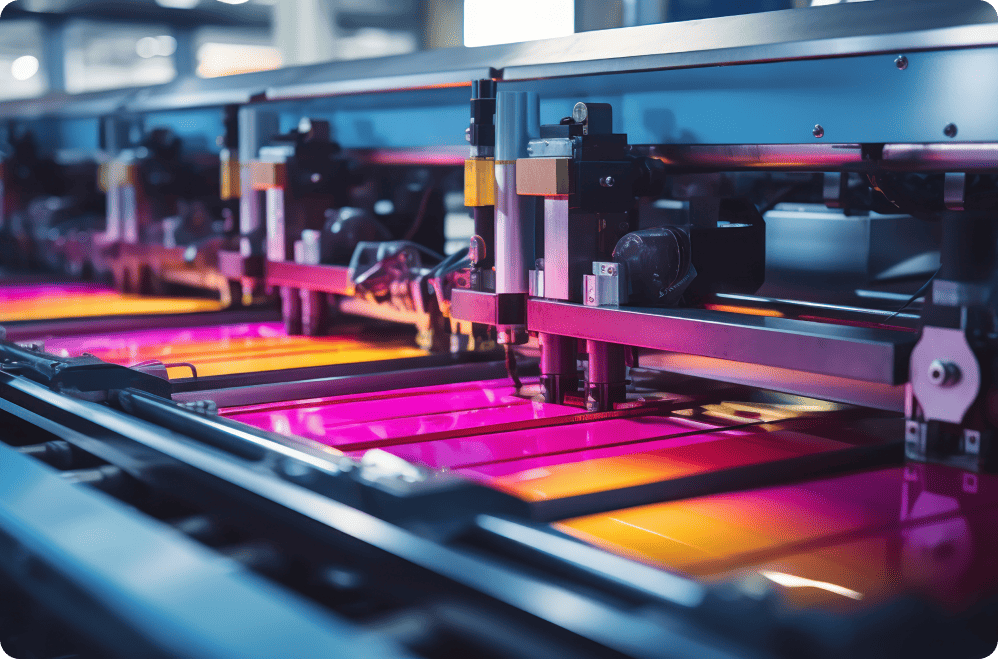
Our client undertook multiple projects aimed at enhancing the performance of existing machinery and we adopted a holistic approach to their R&D claim, highlighting various sub-projects. These included improving plastic injection moulding machines, reducing manual intervention in paper rolling machines and cutting machining costs for paper printing equipment. By focusing on refining existing technology rather than purchasing new machines, the client aimed to develop solutions that could be applied to future models. In each case, their innovations built upon the industry baseline, where little information existed on potential improvements, qualifying them for R&D.
Enhancing plastic injection moulding efficiency
The first sub-project focused on improving the flow of pellets through the plastic injection moulding machine, boosting efficiency. The client designed and prototyped a 'collar follower' to integrate into the existing setup. Early prototypes, however, led to pellet contamination, prompting further iterations with different materials. Through this iterative process, the team successfully enhanced the machine’s performance.
Reducing maintenance in paper rolling machines
The second sub-project aimed to address the problem of paper sticking to rollers, which caused frequent maintenance disruptions. The client experimented with various materials and roller designs, eventually developing a prototype that significantly reduced the need for manual intervention, streamlining production.
Lowering costs for paper printing machinery
In the final sub-project, the goal was to reduce the manufacturing costs of paper printing machinery while maintaining its functionality. The team investigated the current structure, ultimately developing a lightweight design that reduced costs without compromising on performance or safety. Rigorous testing ensured all health and safety requirements were met.
The results: cost-effective improvements
Each sub-project successfully enhanced the functionality and efficiency of the client’s existing machinery.
Each of our client’s sub-projects—whether improving plastic injection moulding, reducing paper rolling maintenance, or lowering paper printing costs—qualified for R&D tax credits with QLC’s guidance. This crucial funding allowed the company to reinvest in more cost-effective innovations, strengthening their competitive edge in the manufacturing industry
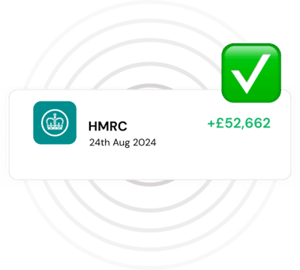
Success stories
What Our Clients Say About Us
"I am really impressed with the efficiency of your work, and the results you got for our company. A very friendly, committed and obviously hardworking team. You made the whole process very easy."
Will Tompkins (Director)
Vintage and Classic Cars
"QLC successfully claimed credits for the past 2 financial years, this year was even better. They managed the application and claimed the R&D credit prior to our annual tax bill, making the whole process quicker, easier and more efficient than last year."
Andrew Forbes (Director)
Architecture
"A massive thanks to all your team, obviously with the current situation, this money couldn’t have come at a better time."
Ian Cooke (Director)
Engineering
"From our experience we have always found QLC to be efficient and thorough in their tax appraisals, carefully guiding us through the often complex process. They have a very approachable team, all of which have been able to offer excellent advice when needed."
Ben Reed (Director)
Architecture
"They are proactive and efficient in performing their service and I have been impressed by their dynamism."
Chris Wright (Director)
Motorsport Engineering
"Your company did exactly what you said it would do. It took far less time than the other company that we had used in the past. We are extremely pleased with the outcome."
Adrian Smith (Company Sec)
Manufacturing Firm
"I am really impressed with the efficiency of your work, and the results you got for our company. A very friendly, committed and obviously hardworking team. You made the whole process very easy."
Will Tompkins (Director)
Vintage and Classic Cars
"QLC successfully claimed credits for the past 2 financial years, this year was even better. They managed the application and claimed the R&D credit prior to our annual tax bill, making the whole process quicker, easier and more efficient than last year."
Andrew Forbes (Director)
Architecture
"A massive thanks to all your team, obviously with the current situation, this money couldn’t have come at a better time."
Ian Cooke (Director)
Engineering
"From our experience we have always found QLC to be efficient and thorough in their tax appraisals, carefully guiding us through the often complex process. They have a very approachable team, all of which have been able to offer excellent advice when needed."
Ben Reed (Director)
Architecture
"They are proactive and efficient in performing their service and I have been impressed by their dynamism."
Chris Wright (Director)
Motorsport Engineering
"Your company did exactly what you said it would do. It took far less time than the other company that we had used in the past. We are extremely pleased with the outcome."
Adrian Smith (Company Sec)
Manufacturing Firm
How much could you claim?
The average R&D tax claim in the manufacturing sector
For your own quick estimate, you can use our easy-to-use R&D tax calculator:
£ 47 k
Common R&D activities in the manufacturing sector
Below is a comprehensive list of R&D activities in the manufacturing sector that may be eligible for R&D tax relief in the UK.
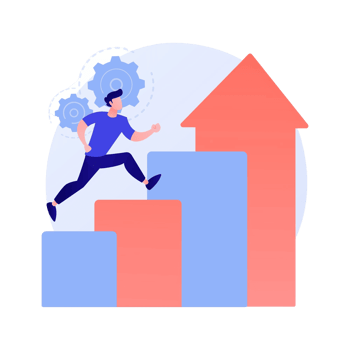
Process Innovation and Improvement
Designing new manufacturing processes
Developing novel processes to improve efficiency, reduce waste, or achieve higher quality in production.
Lean manufacturing techniques
Innovating in process design to reduce waste, improve workflow and optimise resource use.
Continuous process improvement
Implementing incremental or breakthrough changes to enhance existing production processes, including Six Sigma or Kaizen methodologies.
Process automation
Integrating robotics or software solutions to automate previously manual production tasks, reducing human error and increasing consistency.
Custom tooling development
Creating bespoke tools, jigs, or fixtures to solve specific production challenges or improve machine performance.
Product Design and Development
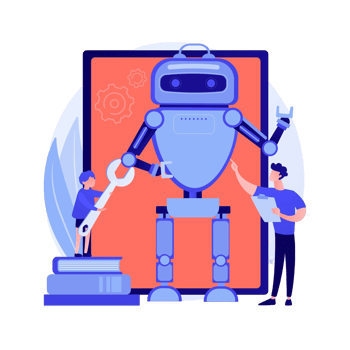
Prototyping and testing new products
Developing and testing prototypes, especially where the process involves resolving technical uncertainties.
Enhancing product durability or performance
Researching and developing ways to improve the lifespan, reliability, or functionality of a product.
Custom product design for specific applications
Tailoring products to meet unique customer specifications, often involving new materials or novel manufacturing techniques.
Material substitution
Replacing traditional materials with lighter, stronger, or more sustainable alternatives without compromising performance.
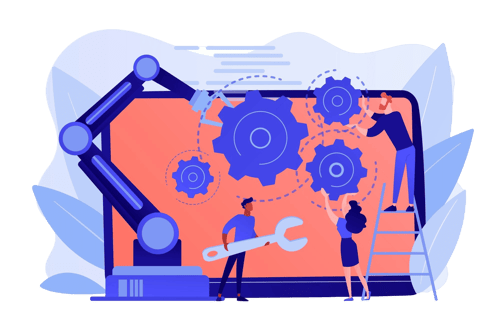
Machinery and Equipment Enhancement
Modifying existing machinery
Enhancing existing machinery to improve efficiency, increase capacity, or extend its operational life.
Integration of new technologies
Incorporating new technologies, such as sensors, data analytics, or machine learning, into manufacturing machinery to optimise performance.
Development of custom machinery
Designing and building new machines or significant modifications to existing ones to solve specific production challenges.
Energy efficiency improvements
Innovating to reduce the energy consumption of production equipment and processes.
Material Science and Development
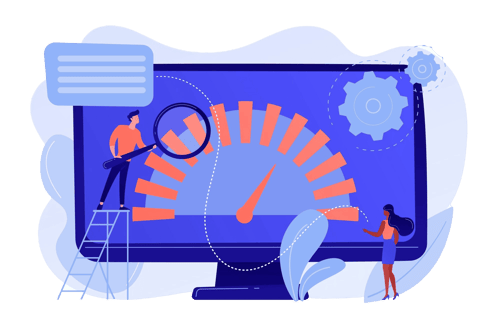
Development of new materials
Creating or adapting new materials (e.g., composites, polymers, alloys) that offer better performance, reduced weight, or improved sustainability.
Testing material properties
Conducting experiments to determine how materials behave under different manufacturing conditions (e.g., stress, temperature, or pressure).
Recycling and waste reduction
Researching methods to recycle or reuse byproducts and waste materials from the production process.
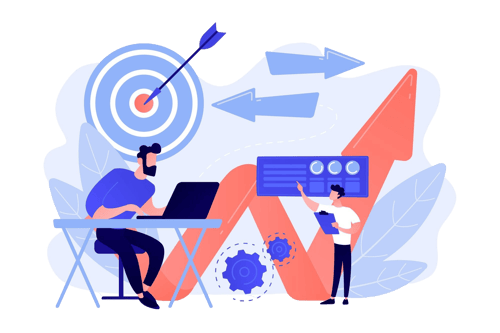
Advanced Manufacturing Techniques
Additive manufacturing (3D printing)
Innovating with additive manufacturing methods to produce complex components that are difficult or impossible to manufacture using traditional methods.
CNC machining advancements
Improving CNC machining processes to achieve greater precision, reduce cycle times, or improve material utilisation.
Digital twin technology
Developing digital replicas of manufacturing processes or equipment to simulate performance, identify inefficiencies and test potential improvements.
Software Development for Manufacturing
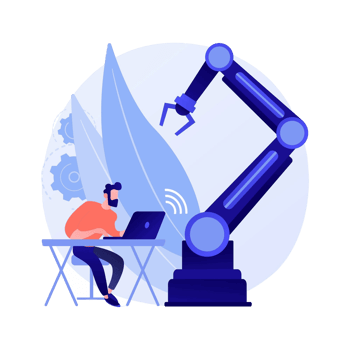
Development of process control software
Creating or enhancing software to monitor and control production processes in real-time, improving efficiency and reducing downtime.
Simulation and modelling
Developing software tools to simulate manufacturing processes, enabling manufacturers to test changes or new designs without disrupting production.
Data analytics for process optimization
Implementing machine learning or artificial intelligence (AI) to analyse production data and identify opportunities for efficiency gains.
Supply chain integration software
Developing solutions to better integrate suppliers and production lines, enhancing just-in-time manufacturing capabilities.
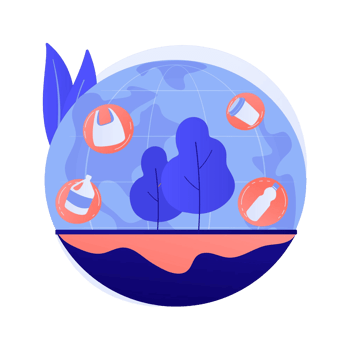
Sustainability and Environmental Improvements
Reducing environmental impact
Developing methods to reduce emissions, decrease water usage, or minimise waste in the production process.
Sustainable material sourcing
Researching ways to incorporate recycled or sustainably sourced materials into production without sacrificing quality.
Designing for disassembly
Innovating product designs to make them easier to disassemble and recycle at the end of their lifecycle.
Quality Control and Assurance
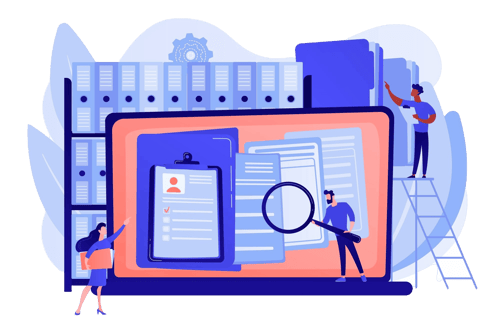
Advanced quality control systems
Developing new technologies or processes to enhance quality control, such as integrating real-time monitoring or automated inspection systems.
Statistical process control
Implementing data-driven techniques to monitor and control manufacturing quality using advanced statistical methods.
Failure mode and effects analysis (FMEA)
Conducting research to predict and mitigate potential product or process failures during manufacturing.
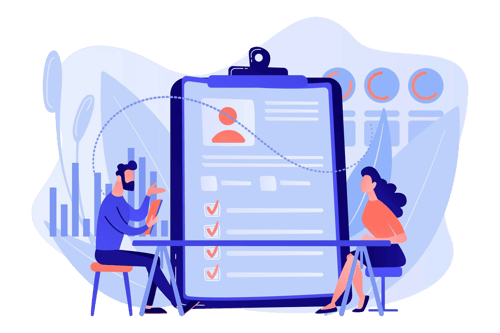
Health and Safety Improvements
Designing safer machinery
Innovating in machine design to meet or exceed health and safety regulations, while improving operational efficiency.
Ergonomic improvements
Developing solutions that reduce the physical strain on workers, such as automation of heavy lifting or reducing repetitive strain tasks.
Workplace safety innovations
Researching and implementing new safety measures, including novel protective equipment or safer production processes.
Supply Chain and Logistics Innovations
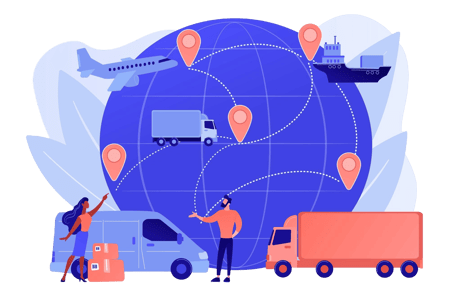
Supply chain optimization
Developing new methods or software to optimise supply chain logistics, improve tracking, or reduce lead times.
Inventory management
Innovating inventory systems to reduce waste, increase turnover, or optimise stock levels based on production schedules.
Just-in-time manufacturing advancements
Researching ways to enhance just-in-time production processes, reducing the need for excess inventory while maintaining production efficiency.
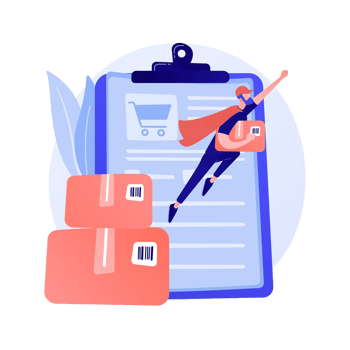
Packaging and Delivery Systems
Innovating packaging materials
Developing new packaging materials or designs that reduce waste, improve product protection, or enhance recyclability.Optimising packaging for shipping
Redesigning packaging to reduce size, weight, or improve stackability for more efficient transport and storage.Automation of packaging processes
Implementing new systems or machinery to automate packaging lines, improving speed and reducing costs.
Energy Efficiency and Emissions Reduction
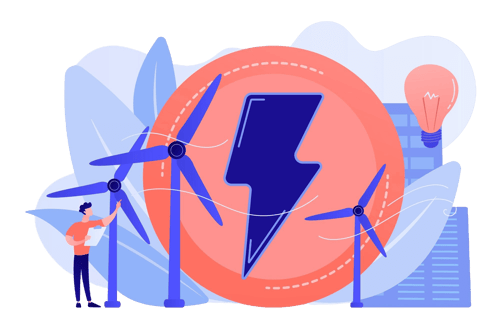
Reducing energy consumption in production
Researching and developing ways to minimise energy use throughout the manufacturing process, including improvements in heating, ventilation and cooling (HVAC) systems.Renewable energy integration
Developing or integrating renewable energy solutions, such as solar panels or wind turbines, into the manufacturing environment.Carbon capture and storage (CCS)
Innovating methods to capture and store carbon emissions from manufacturing processes.
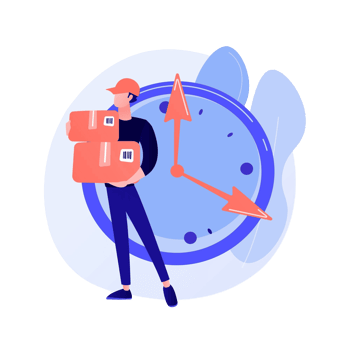
Lean and Agile Manufacturing Techniques
Implementation of agile manufacturing systems
Developing systems that enable quicker changeovers between production runs, improving flexibility and reducing downtime.
Just-in-sequence manufacturing
Innovating methods to deliver parts to the production line in the precise order they are required, minimising handling and storage.
Customization and Mass Customization
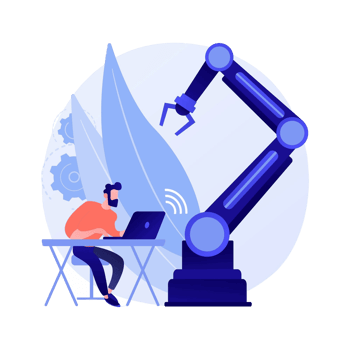
Developing mass customization capabilities
Innovating processes that allow for high-volume production of customised products without sacrificing efficiency.
Flexible manufacturing systems (FMS)
Implementing systems that can rapidly switch between different products or components, enabling more responsive production.
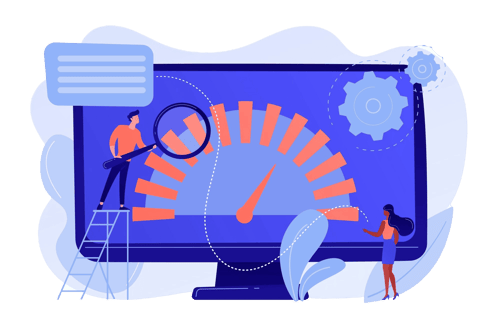
Maintenance and Reliability Improvements
Predictive maintenance
Implementing advanced sensors and analytics to predict when machinery will fail and schedule maintenance proactively.Condition-based monitoring
Developing systems that continuously monitor machine conditions, such as temperature or vibration, to optimise maintenance schedules.Improving machine reliability
Innovating to extend the lifespan of machinery, reduce breakdowns and improve overall reliability through design modifications or new materials.
Waste Minimization and By-product Utilisation
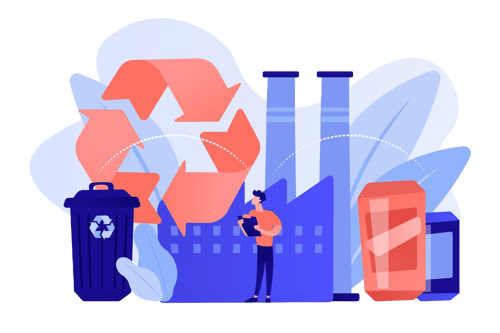
Minimising production waste
Developing new processes that reduce material waste during production, or repurposing waste products for other uses.Recycling of by-products
Researching ways to reuse or recycle by-products of the manufacturing process, such as reclaiming metals or converting waste into energy.Advanced Materials Development
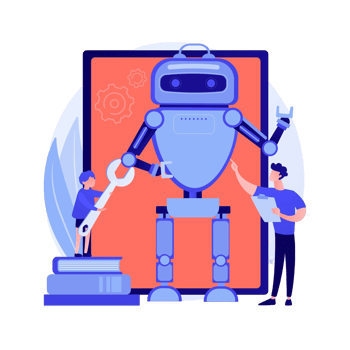
Nanotechnology in manufacturing
Exploring the use of nanotechnology to create materials with enhanced properties (e.g., strength, flexibility, or conductivity).Smart materials
Developing materials that can change properties in response to environmental conditions, such as temperature or pressure, to improve product performance.Why choose QLC?
QLC and our portal help businesses like yours claim R&D tax credits and tax relief faster and more successfully than ever.
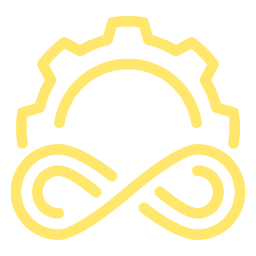
End-to-end service
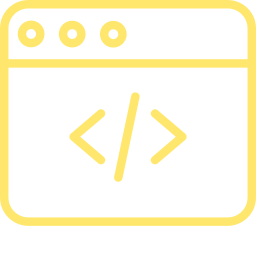
Easy-to-use customer portal
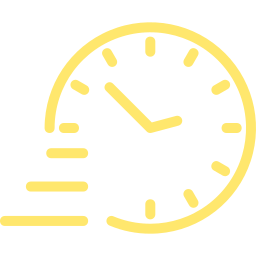
Faster payouts than our competitors
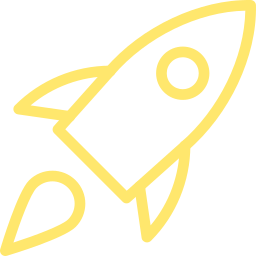
See your money in 16 days
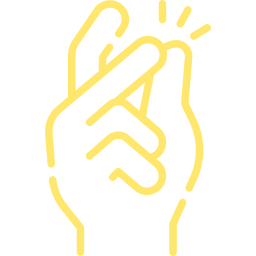
Flexible comms
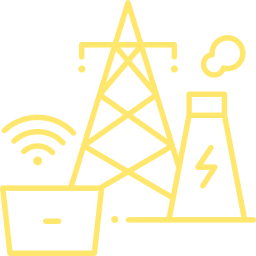
All sectors and sizes
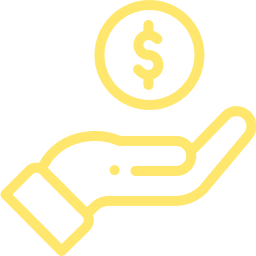
No minimum fee
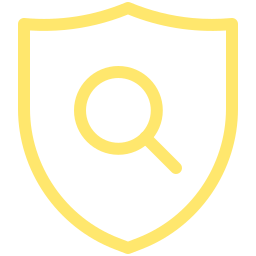
Stakeholder transparency
Manufacturing R&D tax credit FAQ
What types of activities qualify as R&D for tax relief in the manufacturing sector?
R&D in manufacturing can include developing new products, improving existing machinery or processes, creating prototypes, automating manual processes, improving material efficiency, reducing waste and enhancing product durability or performance. Check our comprehensive list above and if you have more questions, get in touch.
Can improvements to existing machinery qualify for R&D tax credits?
Yes, making significant improvements to existing machinery qualifies, especially if the changes enhance performance, efficiency, or longevity in ways that solve technical challenges. This can include modifications that extend the life of equipment, improve throughput, or reduce energy consumption.
Do failed R&D projects still qualify for tax credits?
Yes, unsuccessful R&D projects can still qualify for tax relief. The relief is available for any project attempting to resolve scientific or technological uncertainties, even if the project doesn’t achieve the intended outcome. The focus is on the process of experimentation and innovation.
Can we claim R&D tax relief for custom tooling or jigs developed for manufacturing?
Yes, the development of custom tooling, jigs, or fixtures to solve specific production challenges or improve manufacturing processes can be eligible for R&D tax credits. This is especially true if the work involves overcoming technical difficulties or pushing the boundaries of existing methods.
Can subcontracted R&D work be included in our claim?
Yes, subcontracted R&D work can be claimed, but the amount you can claim depends on whether you are using the SME R&D scheme or the Research and Development Expenditure Credit (RDEC) scheme. For SMEs, subcontractor costs can be claimed at 65% of the total, provided they are directly related to the R&D project.
Form Title
Can developing new production processes be included in an R&D tax relief claim?
Yes, developing new production processes or improving existing ones to increase efficiency, reduce waste, or improve product quality typically qualifies as R&D. For example, automating a manual process, improving workflow, or enhancing energy efficiency may involve overcoming technological challenges that make the project eligible.
How do we claim R&D tax credits if our company has international operations?
Only R&D activities and associated costs incurred within the UK qualify for R&D tax credits. However, you may be able to claim for costs related to overseas subcontractors if they are contributing to a UK-based R&D project. The specific treatment depends on how the work is organised and whether it aligns with UK tax credit rules.
Can software development for manufacturing operations be claimed as R&D?
Yes, developing or enhancing software that supports manufacturing processes, such as control systems, data analytics, or process automation, can qualify for R&D tax relief. This is especially true if the software resolves technical challenges related to improving the efficiency or capabilities of manufacturing equipment.
Are energy efficiency improvements to machinery eligible for R&D tax relief?
Yes, any research or development aimed at improving the energy efficiency of machinery or manufacturing processes can qualify. This includes designing or modifying machines to use less energy, reduce waste, or lower emissions, provided there is a clear technological challenge involved.
Can we claim R&D tax credits for work done on health and safety improvements in manufacturing?
Yes, health and safety improvements that involve overcoming technical uncertainties can qualify for R&D tax relief. For example, developing safer machine designs or improving processes to reduce risks in the production environment could meet the eligibility criteria.
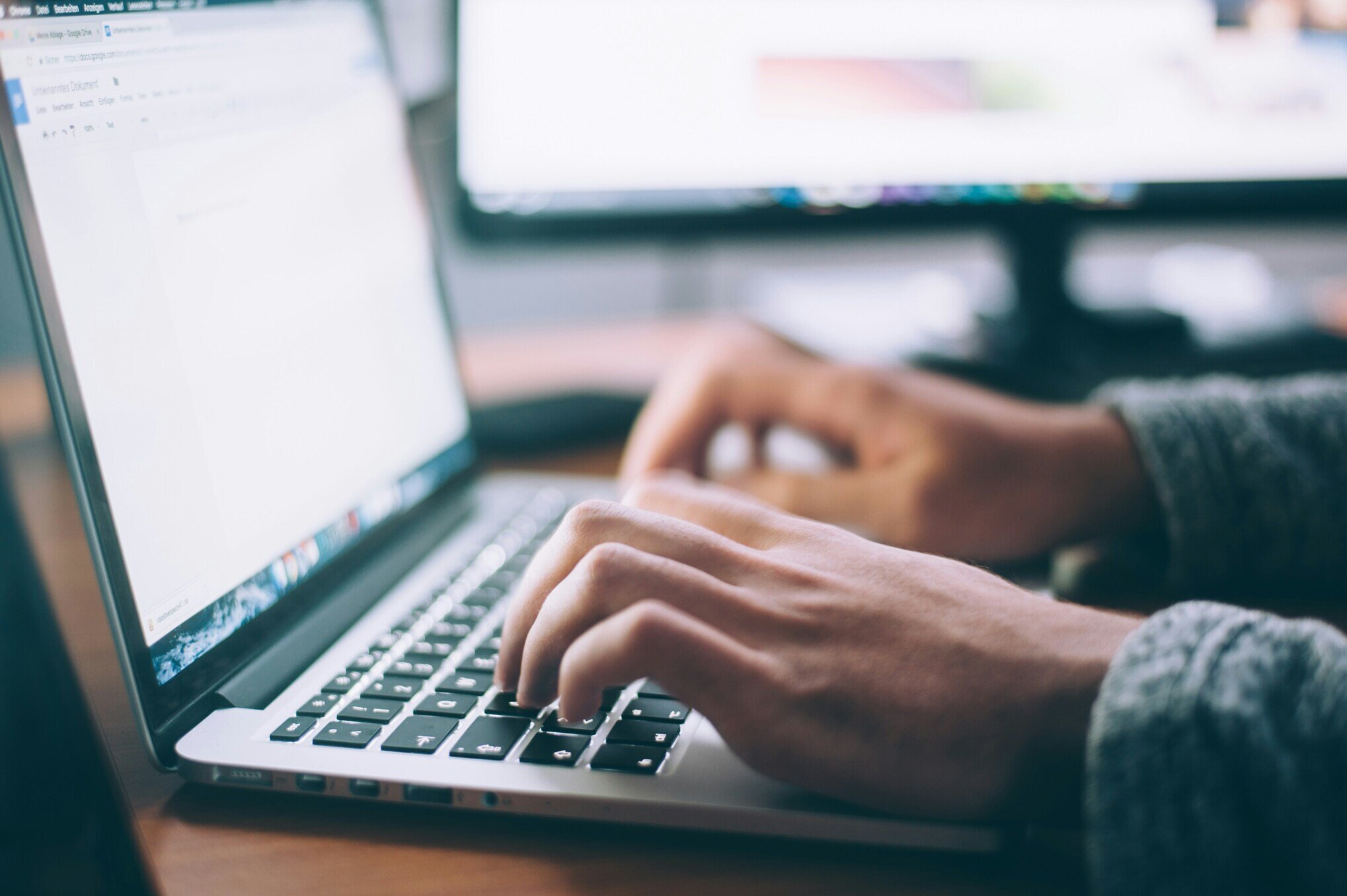
Many manufacturing companies work with specialist advisors like us to ensure they maximise their claims and comply with HMRC’s requirements. Why not get in touch or start a trial of our R&D tax claim portal?